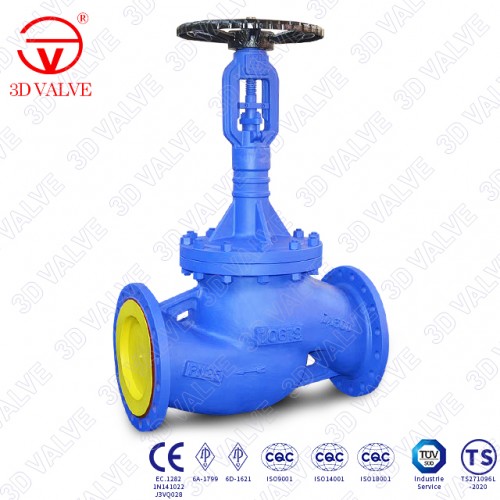
Product overview
Bellow seal valves are normally installed in a working condition that has strict emission requirement and once emission happens it will incur harmful influence to person and environment.This type of valve is achieved by mounting a metal bellow between the bonnet and the stem. Bellow will be driven to scale up and down when stem moves, which will eliminate possible leakage arising from stem movement.
Size: NPS 2"~30"(DN50~DN1650)
Pressure Rating: ASME CLASS 150~1500(PN16~PN260)
Body material:Carbon steel, Stainless steel, Alloy steel, Duplex stainless steel
End connection:RF, BW, RTJ
Operation:Manual, Pneumatic, Electric, Hydraulic
Bellow Seal Valve, also known as bellows seal stop valve, forms a metal barrier between fluid medium and atmosphere through automatic roll welding to ensure the design of zero leakage of valve stem. Bellows structure is adopted inside the Bellow Seal Valve, and the lower end of the stainless steel bellows is welded on the valve stem to prevent the process fluid from etching the valve stem. The other end is placed between the valve body and the valve cover to form a static seal. Double sealing design is adopted. If the bellows fails, the valve rod packing will also avoid leakage. The bellows is welded to the valve rod to maintain stable operation performance and avoid valve rod vibration caused by valve plug vibration. It is most suitable for pipelines with steam, flammable, explosive, heat transfer oil, high purity, toxic and other media. Features of Bellow Seal Valve: 1. Reasonable product structure, reliable sealing performance and beautiful appearance; 2. The sealing surface is overlaid with Co based cemented carbide, with good wear resistance, corrosion resistance, friction resistance and long service life; 3. The valve rod is subject to quenching and tempering and surface nitriding treatment, with good corrosion and friction resistance; 4. Right angle German standard Bellow Seal Valve has double sealing and more reliable performance; 5. Valve rod lifting position indication, more intuitive; 6. Part material, flange and butt welding number and size can be reasonably selected according to actual working conditions or user requirements to meet various engineering needs.